Tighten self tapping screws for plastic, what torque is suitable
Tighten self tapping screws for plastic, what torque is suitablePlastic self-tapping screws are a common method of tightening and assembly. Compared with other connections, the connection has the advantages of low cost, simple process, and reliable connection.
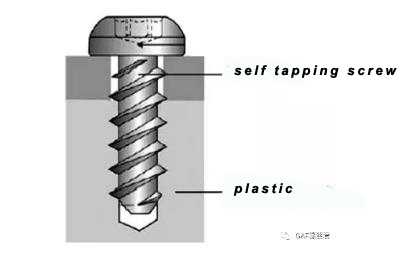
During the tightening process, on the premise that the connected part is not pre-threaded, and hole is drilled by self tapping screw , and then the tightening process is realized. The connection structure
is shown in the following figure, self-tapping screw for plastic is made of general metal material, the hardness can reach 10.9 grade bolts, generally 320-370HV, the connected parts are generally plastic parts, such as PA6-GF material, PBT-GF material, POM-GF material, etc.
Let’s discuss with you guys today: how much torque is suitable for tightening self tapping screws for plastic
There are two main colors of self-tapping screws, black and silver. Electro-galvanized nickel is generally used as the surface treatment, and the strength can generally reach 1000Mpa. Therefore, heat treatment must be used after the screw is formed to ensure the strength of the connection.
Compared with metric bolts with a tooth angle of 60°, self-tapping screws needs to tap the thread in plastic and ensure the connection strength. The tooth angle is generally 30°, as shown in Figure 2

Commonly used sizes are: 2mm-7mm, namely TP2, TP3, TP4, TP5, TP6, TP7, etc. Suppose the diameter of the screw is d. In order to ensure sufficient connection strength, the depth of the threaded hole of the hand is generally recommended to be between 1.7 times d and 2.2 times d.
Because the angle of the screw tapping stage is relatively large, in order to meet the production cycle requirements, the tightening speed of the screw is recommended to be 100-500rpm.
If the overcharge of the tightening tools is serious, the tightening speed can be appropriately reduced, or the tightening can be used in segments, that is, the speed is high first and then the speed is low.
Tightening phase division
(1) Tapping stage
The role of this stage is that the screw taps the thread in the plastic light hole to ensure subsequent tightening. The tapping angle is generally larger, as shown in Figure 3, the tapping angle exceeds 1000°. Therefore, at this stage, the speed of the tightening gun is generally higher, and the highest torque at this stage is the tapping torque. Generally, it is not recommended that the tapping torque is too high.
(2) Fit to the linear maximum torque point
The minimum torque of the straight line of the tightening section is the fitting torque: the maximum torque of the straight line of the tightening section is the linear maximum torque. This section is the position of the process torque point of the plastic self-tapping screw, which is the position where the effective clamping force is generated for the part.
(3) Linear maximum torque to breaking torque point
After passing the linear maximum torque point, the plastic begins to undergo irreversible damage. When the breaking torque is reached, the plastic tightening hole cracks and fails.
(4) After breaking the torque point
The plastic breaks further and the torque starts to decrease until it approaches zero.
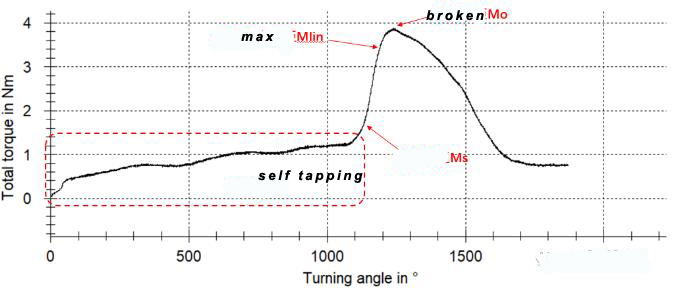
Tighten and repair
If the parts need to be disassembled and repaired, they should be tightened with self-tapping screws one size larger, as shown in the following table.
For example, TP3 screws are used for tightening, and TP4 screws are needed for maintenance.
what torque is suitable
If the tightening torque of the self-tapping screw is too high, it will cause the plastic parts to crack; if the tightening torque is too low, the parts will not be clamped, or even the parts will not fit; therefore, a proper tightening torque is very important.
To this end, we refer to some materials and give the following suggested formulas for your reference:
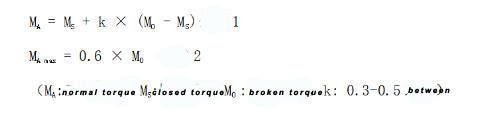
Formula analysis: First of all, it is necessary to ensure that the process torque is greater than the fitting torque. The process torque is based on the fitting torque, plus the fitting torque to 0.3 to 0.5 times the breaking torque.
At the same time, in order to ensure that the plastic parts are not over-tightened, the maximum process torque is not recommended to exceed 0.6 times the breaking torque. Then according to the reference process torque calculated by the formula, the final actual tightening process torque is determined.